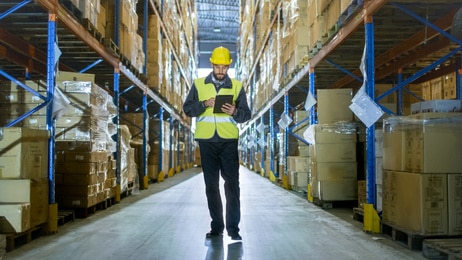
Actuellement, aucun constructeur ne choisit délibérément de faire une offre liée à la maintenance.
Pour une raison très simple, les conditions économiques obligent les acteurs à investir au plus juste et à ne pas faire de projections sur les coûts d’entretien ultérieurs.
La réponse en 2018, c’est oui au quotidien.
Pour faire une vraie prévention de manière économique, nous prétendons que les habitudes doivent évoluer.
La prévention est le meilleur moyen d’obtenir un objectif de maintenance.
Cependant, lors de l’investissement pour l’équipement en rayonnages à palettes, la prévention sera une source d’économies significatives.
Voici un exemple simple pour comprendre comment la conception influe sur les couts de maintenance :
Dans la majorité des cas, les palettes de 800 x 1200 sont stockées en façade 800 mm3 par niveau.
Les constructeurs en s’appuyant sur les Normes ont standardisés des lisses porteuses à 3 palettes avec des jeux de fonctionnement standards.
Le standard pour la majorité des constructeurs est donc de 2700 m ce qui sous entend un jeu entre palettes de 75 mm.
Avez-vous essayé de poser une palette d’une Tonne à 5 m de hauteur avec un jeu entre le matériel et la charge de 75 mm ?
Je peux vous dire que ne pas frotter le matériel de stockage est quasi impossible.
Cela augmente considérablement les risques d’endommager le matériel et peut aussi causer des accidents graves. (Basculement du casier complet, décrochage du niveau, etc…)
Il est possible sans augmenter les coûts d’une installation neuve d’utiliser des lisses de longueur de 2800 mm, ce qui porte le jeu à 100 mm, jeu largement plus sécurisant pour l’utilisateur mais aussi pour le matériel.
Les arguments contre cette méthode de prévention sont essentiellement une occupation plus importante des surfaces dans les bâtiments (avec des loyers très élevés le gain de surface doit être une préoccupation de chaque instant).
Dans la réalité, les installations moyennes ne sont pas impactées ou très peu. Pour en avoir le cœur net, faites des simulations, nous sommes certains que la gène occasionnée sera minime mais la sécurité largement améliorée.
Comme vous le constatez, il est facile d’intégrer la prévention dans la conception d’un entrepôt de stockage, encore faut-il le vouloir et le faire avec des personnes compétentes.
Revenons sur la chaine de valeur d’une installation de stockage.
Comme vous l’avez déjà vu, le transport représente environ 10 % de l’investissement or, lors des réparations, le matériel nécessaire aux réparations sera en petites quantités.
De ce fait, le coût du transport va donc « exploser » (Plus particulièrement pour les éléments longs comme les lisses ou les échelles). Le montant du transport sera alors facilement plus proche de 50 % du prix du matériel pour les réparations.
Cela est loin d’être négligeable. Une solution (si votre entrepôt accepte le stockage de composants neufs) serait de demander dans le cahier des charges un lot « spécial » maintenance. La valeur de celui lors de son achat lors de l’investissement initial sera largement plus économique qu’un achat ultérieur.
La maintenance par la prévention ne serait plus le parent « pauvre » de l’entretien dans les entrepôts.
En effet, la réalisation d’un cahier des charges permettra d’intégrer à bon compte l’entretien qui ne manquera pas de se produire dans la vie d’une installation de racks à palettes.
L’usure des racks est lente, souvent invisible ou cachée sauf si une application numérique est mise en place avec une utilisation systématique, elle vous alertera des visites afin de constater l’état de votre installation.
Moyens de prévention pour les structures de rayonnage à palettes
- Fournir aux fournisseurs un cahier des charges réaliste basé sur une analyse de la fonction demandée pour l’exploitation.
Cela comprendra par exemple, le nombre de palettes à stocker, leur définition la plus précise possible (hauteur, largeur profondeur et surtout le poids réel sans marge de sécurité qu’il faudra « discuter » avec le fournisseur) - Déterminer avec le fournisseur des moyens de manutentions, les largeurs d’allées, la hauteur maxi de dépose.
- S’assurer que le fournisseur à bien pris en compte les sorties de secours en cas d’incendie, les allées piétonnes et/ou les allées de circulation des personnels.
- Orienter l’éclairage perpendiculairement aux rayonnages ou le réaliser au-dessus des allées de circulation. Dans les deux cas, il ne doit pas y avoir de zones d’ombres, toujours causes de mauvaise manipulations involontaires. (Risque de chute des charges sur le personnel)
- Ne pas omettre la zone de réception, expédition, transit ou de préparation .Si celle-ci est mal dimensionnée, les charges vont inéluctablement se retrouver dans les allées, source d’accident potentiels très importante.
En clair, appliquer les recommandations clairement définies dans les documents ED 771 et SP 1120.
La sécurité ne doit pas « pénaliser » une entreprise, au contraire. Il faut donc proportionner les outils de sécurité aux besoins réels. En effet, il ne faut pas comparer un entrepôt de stockage de 100 palettes avec un entrepôt de stockage de 10 000 palettes.
Le bon sens est l’ingrédient indispensable pour intégrer dans l’acte d’achat du matériel de stockage la prévention.
Conclusion :
Non, il ne faut pas dissocier la maintenance et la vente/ou l’achat de racks à palettes métalliques.
Cela coûte nettement plus et les risques d’accidents sont augmentés.